Lean manufacturing
If you want a manufacturing business that’s always improving processes and people, lean manufacturing is for you. Here, we’ll explain some principles and techniques of this method. And then point you in the right direction.
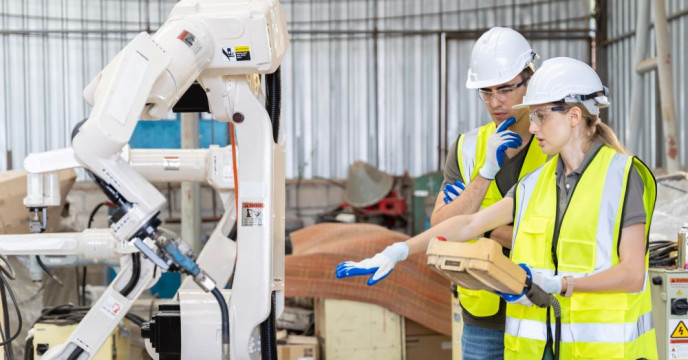
Get rid of unnecessary stuff in your process
Imagine if you could simplify your business so that nothing was wasted, like time, materials, and effort.
Say hello to lean manufacturing – a way of doing business that reduces unnecessary stuff in production processes. Yes, it’s a methodology. But basically, it’s getting more done with fewer resources without sacrificing quality.
Lean manufacturing means you’re always improving
Here’s the thing. It’s not just about streamlining processes. Lean manufacturing focuses you on how to constantly improve. Making small, manageable changes that can lead to big results over time.
Maybe you’re thinking of competing with the rest of the world. Or maybe you are already successful overseas but are looking for ways to maintain your edge. Constantly improving your processes, building your people’s skills and growing some great leaders will get you there.
Lean helps you be flexible
The goal of lean manufacturing is to create a more flexible, responsive, and cost-effective business. It’s worked for businesses all around the world.
Find what’s not working, get rid of it (or at least minimise it), and reap the benefits – better profitability and happy customers who get what they need.
Lean manufacturing can also help you:
- improve quality performance
- increase productivity
- boost employee satisfaction and morale
- reduce production and response time.
The good thing is, lean manufacturing is adaptable. So you don’t need to invest heaps of time, money and resources.
How to use lean manufacturing
Follow these steps to improve a process using lean manufacturing.
- Identify the problem or opportunity you want to improve.
- Choose the best lean manufacturing technique based on the context.
- Form a team that has the range of skills needed.
- Collect and analyse data on what’s happening now.
- Develop and put in place the strategies to improve.
- Monitor the results and adjust anything if needed.
- Celebrate the success!
Watch: Technology for cutting costs and minimising waste in manufacturing
transcription
Video transcript: Technology for cutting costs and minimising waste in manufacturing
[Video begins. A mid-shot of a man in a black suit jacket with a patterned blue button up seen underneath. The man stands in a factory, blurred out behind him. He speaks directly to the camera.]
Speaker: Kia ora and welcome to the future of manufacturing in Aotearoa, where we showcase how Industry 4.0 technologies can help you minimise waste, save time, money and become a more sustainable manufacturing process.
[The screen changes again to show two men, standing beside a hologram of a car split into various parts. An engine twists into visibility within the hologram and the men look closely at it as the speak to each other. The screen changes again to an over the shoulder shot of a man looking at a tablet, sat on a bench in front of him. There is also another man in the background, only slightly visible and not in focus. The man looking at the tablet taps the screen with an e-pen, causing the image of a desk on the screen to change and spread into all its individual parts. The screen changes briefly to a robot quickly screwing a bolt into a mechanical part. The screen changes again to a mid-shot of a woman wearing high-visibility gear and a hard hat is tapping the air out in front of herself. She has a VR headset on. The screen changes to a high angle shot of a man in blue scrubs and black gloves working on a desktop beside a heavy-duty machine. The screen changes again to a close-up of a computer screen. On the computer screen we see 4 gear boxes beside each other with model information to the right of them.]
Speaker: Industry 4.0 is the Fourth Industrial Revolution. It's the integration of digital tech into manufacturing businesses using tools like automation, AI, the Internet of things, and data to improve the way we work.
[Screen reverts to the mid-shot of the speaker.]
Speaker: This new wave of technology isn't just about making things more efficiently, it's about making them safely and sustainably too. First let's define what we mean by waste in the context of lean manufacturing. Waste refers to any activity that doesn't add value to the final product for example…
[The word “Overproduction” appears to the left of the speaker as he says the word. It remains for a few seconds by being replaced by “Waiting”, which is then replaced by “Transport”, replaced by “Overprocessing”, replaced by “Inventory”, replaced by “Motion”, replaced by “Defects”.]
Speaker: Overproduction: making more products than needed which can lead to storage and maintenance costs.
Waiting: time wasted when workers or machines are idle waiting for a precious step to be completed. Transport: unnecessary movement of materials or products which can cause damage or delays. Over-processing: doing more work or a higher quality work than is necessary which uses up resources and time. Inventory: excess raw materials, work in progress, or finished goods that tie up capital and space. Motion: unnecessary movements by workers such as walking or reaching for tools which can lead to inefficiency and injuries. Defects: products that don't meet quality standards and require rework or disposal.
[Screen changes to a large, yellow, triangular machine part attached to a wheel, which is connected to a conveyor belt tape. The triangle rotates as the wheel with the conveyor belt tape. The screen changes again to a series of cylinders whirring. The screen changes again to a close up of a beam being pulled out of square opening. The shot changes to the same location but further back, showing the man who had been pulling the beam as he picks it up and carries it over to hand to someone out of shot above a series of beams. The person out of shot then gets ready to screw a nail into the fresh beam onto the other beams. The shot changes again to a high angle shot of a man using a desktop against a wall against heavy-duty machinery. The screen changes again to another machine. This is a close shot. The camera closes in on a flat compartment of the machine, to show a moving part within this flat compartment. The screen changes back to the same man who had been using the desktop against the wall, only he is now walking up to a small door within the machinery. He opens the door and takes out a lunchbox shaped object. It is cream coloured with a red lid, only a circle is missing from the centre of it.]
Speaker: The goal of lean manufacturing is to identify and eliminate these types of waste and improve efficiency and quality. This way companies can save money and deliver better products to their customers and technology can help enormously. Collecting data at source and using predictive data analytics tools can improve forecasting which can help with parts or ingredients ordering, avoid under or over-production, and reduce downtime for your machines and your people.
[Screen reverts to the mid-shot of the speaker.]
Speaker: This is often coordinated by a manufacturing execution system, MES, which gathers, analyses, and displays data they help people make decisions in real time and improve efficiency and effectiveness of the factory.
[The screen changes to an establishing shot of the Breadcraft brand on a wall. The word “BREADCRAFT” is in big red letters with a graphic of a man in the chef’s hat and a yellow scarf on a red semi-circle above. On either side of the graphic are wheat grain graphics. The screen changes to a large conveyor belt, as tortillas move along the conveyor belt, through a metal divider, onto another conveyor belt. The screen changes to a high angle shot of a scanner above stacks of tortillas as the move along on a conveyor belt. The screen changes to a screen showing a machine dropping the tortilla dough onto a red conveyor belt. The screen changes back to the tortillas being scanned but from a wider angle, showing more than just the one scanners and multiple stacks of tortillas. The screen then changes to a screen showing the tortillas being processed by a scanner. Good tortillas have green squares pop up over them and bad tortillas have red squares pop up over them, as they move through the conveyor belt and are scanned. The screen then changes to a shot of an arm holding out a tablet. On the tablet shows a data set reviewing the performance of productivity. The screen changes to a shot of shelves of blue conveyor belts moving in alternate directions. The screen changes again to a high angle shot of the stacks of tortillas being pushed by metallic prongs into plastic packaging. The screen changes to a shot of the packaged tortillas moving quickly along a conveyor belt.]
Speaker: Take Breadcraft as an example of a business using these tools in its daily operations. With vision cameras and sensors for real time monitoring they quality control their tortilla production line ensuring only perfect tortillas pass. This eliminates human error and provides consistent product quality the data they pull from these tools gives them critical insights for optimising operations - enabling continuous adjustments.
[Screen reverts back to the mid-shot of the speaker.]
Speaker: The result? Less waste, more efficiency, and a friendly nudge to their bottom line. Next, let's talk about energy efficiency. Smart sensors can help to reduce energy consumption. They can monitor a machine's energy consumption in real time. This data can point out where energy is being used inefficiently and allows the operation schedule to be adjusted.
[Screen changes to a mid-shot of a man in a high-visibility jacket and a hard hat. He holds a tablet and is observing a machine with lots of buttons of various sizes and shapes with a screen showing tiny words and numbers that aren’t visible in the shot. The screen changes again to a machine, with an arm of the machine moving about above a flat material. The moving arm seems to be making markings on the flat material. Sparks fly as these markings are made. The screen changes again to a man sat down on an office chair. He wears a heavy-duty jacket, as he uses a keyboard to move camera views on security cameras, the point of view seen through a screen in the top left of the shot.]
Speaker: Smart sensors can also improve maintenance, for example, collecting temperature, vibration, and energy consumption data. It can predict equipment failures before they occur or even reduce the routine maintenance that may not actually be required.
[The screen reverts to the mid-shot of the speaker.]
Speaker: Another common challenge is inefficient transport routes leading to increased fuel consumption and emissions.
[The screen changes to an over the shoulder shot of a man pointing at one desktop screen out of two in front of him. They sit on an office desk, with multiple desktops and workstations visible out of focus within the shot. A woman is stood slightly out of frame to his right. The screen changes to a close-up of the screen. It shows a map with multiple locations highlighted by blue and red circles. The computer screen zooms in, showing more blue and red circles the more it zooms in. The screen changes again, showing a laptop screen and a phone screen beside one another with a white background. Both the laptop and phone show the same visuals – a map with red dot at one end of dark blue route line and a black pin-point at the other. The screen changes to a scenic shot of Auckland bridge. You can see the Auckland city-scape along the top half of the screen. The screen changes to a different angle of the bridge. It shows a closer view of the bridge running left to right of the shot. You can see multiple cars driving both up and down the bridge.]
Speaker: By using GPS tracking and route optimisation software, manufacturers can analyse various factors like traffic patterns, fuel efficiency, and delivery schedules to optimise their transportation routes. By choosing the most efficient routes, minimising empty truck miles, and consolidating shipments, businesses can reduce fuel consumption, lower emissions, and cut down on transportation costs.
[The screen reverts to the mid-shot of the speaker.]
Speaker: In summary, by embracing Industry 4.0 technologies, Kiwi manufacturers can minimise waste, improve efficiency and grow revenue, all while helping to build a safe and sustainable future for generations to come.
[Screen changes to show the webpage “Industry 4.0 Case Studies” on the EMA website and scrolls down the screen slightly.]
Speaker: Visit the EMA website for manufacturing case studies and webinars. Learn from experts and local businesses to make your business more resilient and profitable.
[The screen reverts to the mid-shot of the speaker.]
Speaker: Go to industry4.ema.co.nz
[Screen changes to a blue background with white text reading “Thanks to BECA for their technical advice”; next line: “EMA”; next line “For more information on Manufacturing industry ema.co.nz”. Music swells.]
[Video ends.]
Five main principles to practise lean manufacturing
Lean manufacturing is a mindset – a way of thinking. Grasp these five main principles and apply them as a whole to start practising Lean.
- Value stream mapping – visualise and map out your whole production process to find out what’s not working or inefficient.
- 5S (Sort, Set in order, Shine, Standardize, Sustain) – organise your workplace to be super-efficient and safe by following the five steps.
- Just-in-time production – produce only what’s needed, when it’s needed, so you don’t have expensive inventory and workers waiting around.
- Continuous improvement (often called Kaizen) – encourage ongoing improvements that involve all employees, even up to top management.
- Pull systems – produce products when the demand is there (the pull), so you don’t overstock or overproduce.
Lean manufacturing tools and techniques
Lean manufacturing offers a range of tools and techniques. You might use different ones depending on your business. Here’s a handful of the most popular techniques.
Six Sigma
Measure your processes, then use the data to see where you can reduce variations – that’s anything unexpected or uncontrolled. Motorola brought this popular technique to the world in the 1980’s.
Six Sigma uses five stages to solve these problems in processes – Define, Measure, Analyse, Improve, Control (DMAIC).
Total Quality Management (TQM)
Constantly look to improve processes and keep customers satisfied. You involve all employees and make sure they’re well trained.
Theory of Constraints (TOC)
Manage the main thing that’s causing a problem or holding things back in a process to improve performance.
Plan-Do-Check-Act (PDCA) cycle (sometimes known as Deming Cycle)
Follow this cycle of steps to continuously work out what’s working in your processes and what’s not.
Automation can be helpful, but check if you need it
Lean manufacturing can mean adding advanced tech to your processes. If that’s the case, it’s super important to fully understand your processes and what tools you need for what tasks.
Check if automation will move your business forward. Ask yourself:
- Does that task need to be automated?
- Will that fancy new tool give me value in the long term?
- Will that investment sustain the business for a long time?
Technology changes quickly. To keep flexible, you want to invest in a tool that’s still going to do the job if things change, such as customer needs, your business model, or your processes.
Get started with Lean
Well, all that info’s great, but where do I start?
Advanced Manufacturing Aotearoa (AMA) is a great place to start. They’re on a mission to help manufacturers up their game.
They want you to improve your productivity and output. And that means by adopting smart and modern technologies and process, so that you’re more productive, sustainable and globally competitive.
And they have regional support groups throughout the country. Check in with AMA to see what’s available where you are.
AMA — Advanced Manufacturing Aotearoa
Related topics
Improve your productivity
Stay competitive by continuously improving your business operations. There are four main ways to do so. Find out how they can work for you.
Industry 4.0 and strategic planning
Industry 4.0 is changing the manufacturing scene. Learn what this means for you, how to plan and successfully transition into the future.