Careers in manufacturing
People with all kinds of skills are needed in the fast-changing manufacturing sector. Find out how you as an employer can help them start and grow their careers.
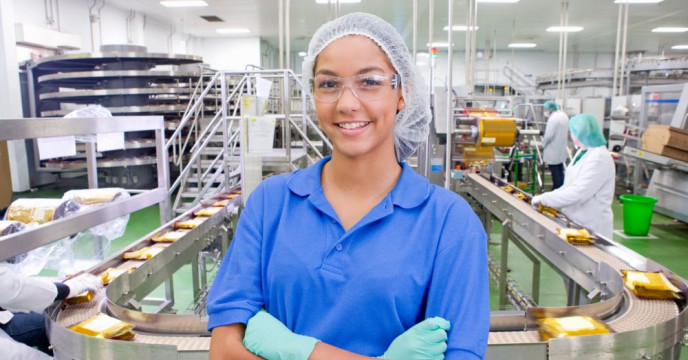
Helping your people learn makes your business stronger
New Zealand manufacturers are competing on the world stage and winning! But it’s a team effort.
Great employees are gold to a business. They’re productive and efficient, and they stick with you. They’ve got the know-how you need. And if there’s something they don’t know, they’re keen to fix that.
So how do you get these people into your business? Easy. Help them grow. Give them the resources, equipment and support they need to learn and become the best they can be.
It’s a win-win. You help your employees become even more confident, highly skilled and satisfied. And your employees help put your business in a better position to survive and thrive.
Manufacturing is evolving and needs specific skills
The revolution is here – Industry 4.0
Most manufacturing is still human-powered. So, the push for Industry 4.0 by manufacturing leaders means your team can quickly gain valuable knowledge and insights. And they can work with the new technologies, robotics and automation that come with Industry 4.0.
Work smarter, not harder
Give your team the tools they need to make their day easier and the know-how to boost efficiency in your operations. In turn, that puts you in control, automates all the boring stuff and helps you go beyond your customers’ expectations.
Two things will help you stay on top of it
They’re both do-able.
- Equip your people with the skills that will help your business transition and grow.
- Get in touch with tertiary and workplace educators to help bring those skills into your business, understand what’s new and prepare for what changes are coming. And then stay in touch.
Help train your people
Manufacturing is an attractive career choice. It offers a pathway to earning competitive wages, working flexible hours and getting involved in exciting projects. And it’s an industry where you can help people grow personally and professionally in a rewarding career.
There’s a pathway for everyone
No matter the skills, experience or qualifications, there’s a pathway and an entry point for most people in manufacturing. You can start people off as an apprentice and help them work their way up. Or they can jump in at a more specialised level with experience, skills or qualifications.
The industry is super keen to grow talent, so there are also plenty of innovation programmes on offer – from intern to senior leadership level. They’re perfect for people to showcase and use their skills in the manufacturing world.
Work out what expertise you have and what you’ll need
When you know what skills and abilities your people already have and what you need in the future, you can identify gaps. Then help your people to learn how to get the skills to fill those gaps. As your business invests in new technologies, robotics and automation, people can move to new areas of need and further expand their skills and abilities.
Use our list of roles and career pathways in manufacturing to guide you.
Connect with trainers and providers
Connect with tertiary and training institutions and workplace education providers to find out:
- what’s changing in manufacturing
- what skills and knowledge are needed to keep up with that change.
Info for employers about tertiary and workplace education — Tertiary Education Commission
Strengthening the manufacturing, engineering and logistics industries — Hanga-Aro-Rau Workforce Development Council
Create a learning and skills development policy
Writing policies isn’t everyone’s idea of fun. But having a learning and skills development policy shows that you’re serious about helping your people. Make life easier and use our Workplace Policy Builder tool to whip up a customised learning and skills development policy for your business.
It’s easy to use and it guides you through each step to create your policy.
Workplace policy builder tool — business.govt.nz
-
Production and operations
Machine operators
- Operate, set up and maintain machinery used in the manufacturing process.
- Normally train on the job, although more qualifications might get you a better role faster.
Assembly line workers
- Assemble parts or products to make sure quality and production targets are met.
- Work in industries like electronics, plastics or food processing.
Team leaders / production supervisors
- Oversee production lines, manage staff and ensure efficiency and quality control.
- Are better off if they have a background in operations management or hold relevant trade qualifications.
-
Trades and technicians
Welders, fabricators and fitters
- Construct machinery, equipment and infrastructure.
- Can start off as apprentices or with trade qualifications in welding, mechanical engineering or fitting and turning.
- Can progress to Stainless Fabricator Welding Certificate 6G positions after 3-4 years.
- Can get American Society of Mechanical Engineers (ASME) welding certification, but welding and fabrication companies must meet quality and safety standards.
Welder Qualifications(external link) — Weldtest New Zealand
Electricians and maintenance technicians
- Install, maintain and repair electrical systems in manufacturing plants.
- Are crucial to minimising downtime and ensuring smooth operations.
Computer Numerical Control (CNC) operators and programmers
- Operate and configure advanced machinery to product precision parts.
- Normally need training in mechanical engineering or CNC programming.
Computer Numerical Control (CNC) engineers
- Do CNC programming (and be able to program multi axis machines).
- Programming must be taught in house or outsourced.
- Apprentices must do general engineering apprenticeships (manual machining) instead of computer numerical control machining.
-
Quality control and assurance
Quality control
- Test, measure and evaluate production processes to maintain consistent quality. This makes sure products meet industry and company standards.
- Need a knowledge of industry standards and regulatory requirements.
Quality assurance managers
- Design and implement quality systems that govern the production process.
- Often need a background in engineering or manufacturing with an emphasis on quality standards like International Organisation for Standardisation (ISO), for example, Quality Systems – ISO 13485/ISO 9001 or Lean Six Sigma.
-
Engineering
Mechanical engineers
- Design, develop and improve manufacturing systems, machines and tools in industries like machinery and aerospace.
- Normally need a bachelor’s degree in mechanical engineering.
Mechanical Design engineers
Normally need a bachelor’s degree in mechanical engineering or equivalent.
Process engineers
- Improve efficiency, reduce costs and enhance production processes.
- Often need a background in chemical or industrial engineering.
Computer Numerical Control (CNC) engineers
- Design and maintain the electrical systems and machinery used in manufacturing.
- Increasingly need expertise in smart technologies with the rise of automation and Industry 4.0.
-
Logistics and supply chain management
Logistics and coordinators
- Manage the supply chain and ensure the smooth flow of raw materials into the production process and finished goods to consumers.
- Need to have skills in inventory management, supply chain optimisation and logistics software.
Warehouse managers
- Oversee storage, distribution and inventory management, ensuring efficient operations in manufacturing environments.
- Have an advantage if they have experience in logistics or warehouse operations.
-
Research and development (R&D)
R&D scientists and engineers
- Develop new products, materials and processes.
- Often need a strong background in science, particularly in chemistry, physics or materials science; and experience in the specific manufacturing industry.
Product development managers
- Develop new products from concept to market and coordinate between design, engineering and manufacturing teams.
- Often need a background in project management or product design.
-
Automation and Industry 4.0 roles
Automation technicians
- Are in high demand if they can install, maintain and troubleshoot these systems – especially with robotics and automated systems becoming more integrated in manufacturing.
Data analysts
- Optimise production efficiency, reduce waste and predict maintenance needs.
- Are increasingly employed by manufacturing companies with the rising focus on data-driven decision-making.
Robotics engineers
- Design and develop robotic systems used in the manufacturing process.
- Are normally needed for their expertise in robotics, computer programming and mechanical engineering.
-
Management and leadership
Production managers
- Oversee all aspects of the manufacturing process, and ensure it operates smoothly, safely and efficiently.
- Have an advantage if they have a background in manufacturing or industrial management.
Operations managers
- Manage the broader functions of manufacturing, including production, logistics and quality control.
- Often need a degree in business, engineering or operations management.
Plant managers
- Take responsibility for the overall performance of a manufacturing facility. This includes personnel management, budgeting and strategic planning.
- Often need a strong background in engineering or manufacturing.
-
Sustainability and environmental roles
Sustainability managers
- Make sure manufacturing practices are eco-friendly and comply with environmental regulations – especially with the increasing focus on environmental responsibility.
- Have an advantage if they have a background in environmental science or sustainability.
Environmental engineers
- Reduce the environmental impact of manufacturing processes, including waste reduction, energy efficiency and pollution control.
- Normally need a degree in environmental engineering.
Related topics
Improve your productivity
Stay competitive by continuously improving your business operations. There are four main ways to do so, and we’ll walk you through them.
Lean manufacturing
Want to improve the efficiency of your people and manufacturing processes? Learn about the principles and techniques of lean manufacturing, and how you can apply them.